Compass Q1 three-wheeled omni-directional platform
Product Briefing
The Compass series is a small fundamental robot platform. It aims to provide users with a complete mobile robot system with high reliability and multiple interfaces. Compass Q1 is a robot platform with three 90 degrees QL-10 omni wheels. Compared with the traditional gear train, the QL-10 omni wheel is able to accomplish many special movements, like translation, rotation, and simultaneous translation & rotation.The chassis of this platform adopts overall aluminum casting & molding process. Compass Q1 uses three high-power coreless motors as the driver, equipped with multi-axis servo driver, supporting both CAN bus and RS232 interface. The development kit provides customers with a complete equipment communication protocol, and also provides examples and demo application source code based on STM32F407, which allows users quickly know how to operate Compass Q1
Video Display
Product Characteristics
- move to all the directions
- overall aluminum casting & molding process
- Industrial grade omnidirectional wheel
- coreless DC servo motor
- servo driver
- demo application source code based on STM32F407
Exterior Dimension
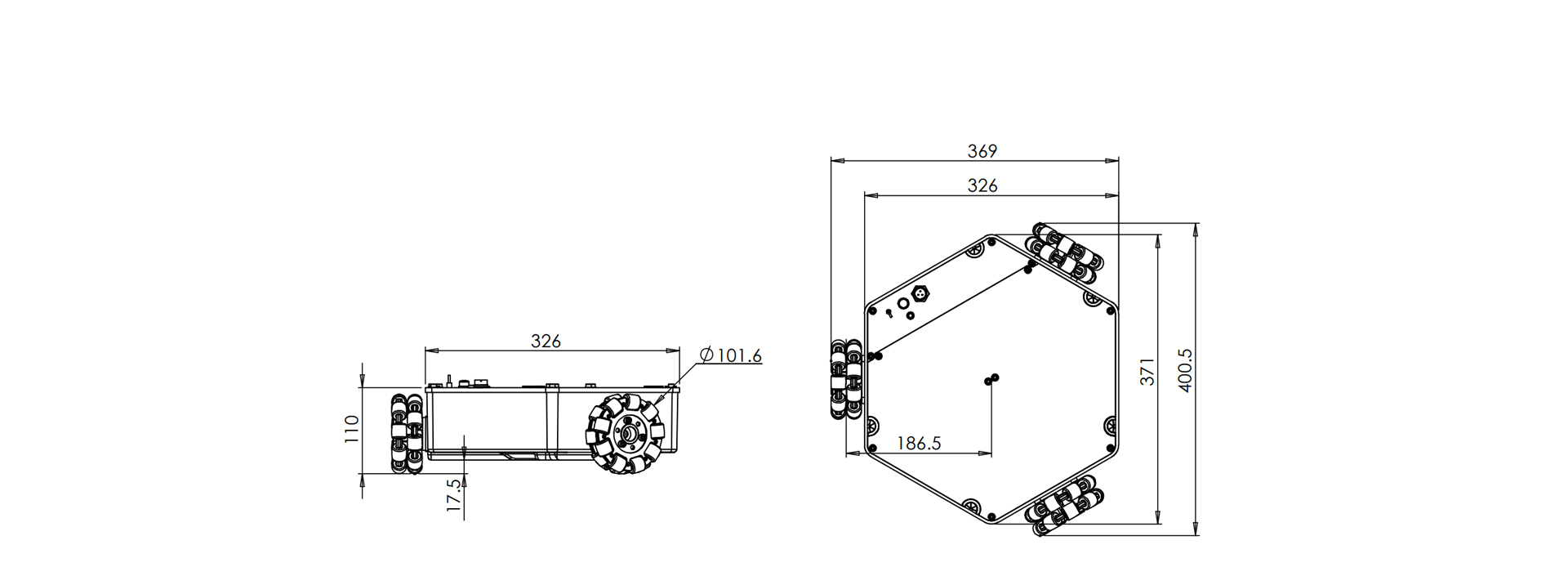
Specification Parameters
Fuselage Form | Aluminum alloy one-piece molding | Overall Dimension | 369×400.5×110 |
Driving Wheel | QL-10 Omni-directional Wheel | Diameter of Driving Wheel | 101.6mm |
Driving Method | Three-wheel independent drive | Suspension Form | No suspension |
Minimum Ground Clearance | 17.5mm | Weight | 7.1kg |
Rated load Capacity | 20kg | Motor Type | Hollow Cup DC Servo Motor |
Motor Rated Power | 30W | Motor Encoder | 500 lines/revolution, A and B phase outputs |
Number of Motors | 3 | Motor Drive | Servo drive, CAN bus, RS232 communication interface |
Maximum Travel Speed | 1.2m/s | Maximum Rotation Speed | 365°/s |
Minimum Turning Radius | 0m | Adaptable Terrain | Indoor and outdoor concrete and asphalt pavements with fewer potholes |
Typical Endurance | Approx. 10h (load 10kg, operating speed 1m/s, operating rate 70%) | Standby Time | >30h |
On-board Power Output | 5V@2.5A / 12V@2.5A / Battery voltage (22.4~29.2V)@>5A | Power Fuse Preset Specification | 5×20/10A |
Battery | 24V/7.8Ah lithium-ion battery | Battery Quick Change | Support |
Charger | Input:AC220V~240V / Charging current:3A / Interface:Plug-in type | Accessory | Battery charger, ULB-1 ultrasonic transducer × 5 |
DEMO Board | RHF407 development board (CAN×2, RS232×2, TTL×1, RS485×1, SPI×1, I2C×1, ADC×8, DAC×2, PWM×8, LED×2, keypad×2, independent I/O×24, reusable I/O×29, TF card interface×1, RTC backup battery holder, reusable TFT LCD interface×1) |
Fuselage Form | Aluminum alloy one-piece molding | ||
Driving Wheel | QL-10 Omni-directional Wheel | ||
Driving Method | Three-wheel independent drive | ||
Minimum Ground Clearance | 17.5mm | ||
Rated load Capacity | 20kg | ||
Motor Rated Power | 30W | ||
Number of Motors | 3 | ||
Maximum Travel Speed | 1.2m/s | ||
Minimum Turning Radius | 0m | ||
Typical Endurance | Approx. 10h (load 10kg, operating speed 1m/s, operating rate 70%) | ||
On-board Power Output | 5V@2.5A / 12V@2.5A / Battery voltage (22.4~29.2V)@>5A | ||
Battery | 24V/7.8Ah lithium-ion battery | ||
Charger | Input:AC220V~240V / Charging current:3A / Interface:Plug-in type | ||
Overall Dimension | 369×400.5×110 | ||
Diameter of Driving Wheel | 101.6mm | ||
Suspension Form | No suspension | ||
Weight | 7.1kg | ||
Motor Type | Hollow Cup DC Servo Motor | ||
Motor Encoder | 500 lines/revolution, A and B phase outputs | ||
Motor Drive | Servo drive, CAN bus, RS232 communication interface | ||
Maximum Rotation Speed | 365°/s | ||
Adaptable Terrain | Indoor and outdoor concrete and asphalt pavements with fewer potholes | ||
Standby Time | >30h | ||
Power Fuse Preset Specification | 5×20/10A | ||
Battery Quick Change | Support | ||
Accessory | Battery charger, ULB-1 ultrasonic transducer × 5 | ||
DEMO Board | RHF407 development board (CAN×2, RS232×2, TTL×1, RS485×1, SPI×1, I2C×1, ADC×8, DAC×2, PWM×8, LED×2, keypad×2, independent I/O×24, reusable I/O×29, TF card interface×1, RTC backup battery holder, reusable TFT LCD interface×1) |
Typical Components
-
QL-10 omni wheel
-
HFmotor-3230 coreless DC servo motor
-
RHF407 development board
-
ULB-1 ultrasonic range-finding sensors
-
IMDR4 motion controller
Typical Research and Application Areas
- Pattern recognition technology research
- Electronic engineering experiment
- Carrying and storage applications
- Route planning technology research
- Mechanical engineering experiment
- Monitoring and investigation application
- Automatic driving technology research
- Embedded system development and experiment
- The robot competition
- Sensor technology research
- Image process technology research
- Mapping application
- Artificial intelligence research
- Multi-robot cooperation technology research
- Flexible manufactur system application
Optional Accessories
- HMC-1 remote control handle
- LPC-16 patrol sensor
- ULB-1 ultrasonic range-finding sensors
- Laser radar
- GPS locator
- Kinect device body sensor