Compass C1 two-wheel differential platform
Product Briefing
The Compass series is a small fundamental robot platform. It aims to provide users with a complete mobile robot system with high reliability and multiple interfaces. Compass C1 is a robot platform equipped with two HSL-15 inflatable rubber driving wheels and two separately hanged driving wheels, which can adapt to all kinds of working environment and complete all kinds of sports efficiently. The chassis of this platform adopts overall aluminum casting & molding process. Compass C1 uses two high-power coreless motors as the driver, equipped with multi-axis servo driver, supporting both CAN bus and RS232 interface. The development kit provides customers with a complete equipment communication protocol, and also provides examples and demo application source code based on STM32F407, which allows users quickly know how to operate Compass C1
Video Display
Product Characteristics
- Omnidirectional driven wheel
- Independent suspension of driven wheels
- Aluminum alloy integral forming chassis
- Industrial grade rubber wheels, omnidirectional wheels
- Hollow cup DC servo motor
- Servo drive
- DEMO development board and application code
Exterior Dimension
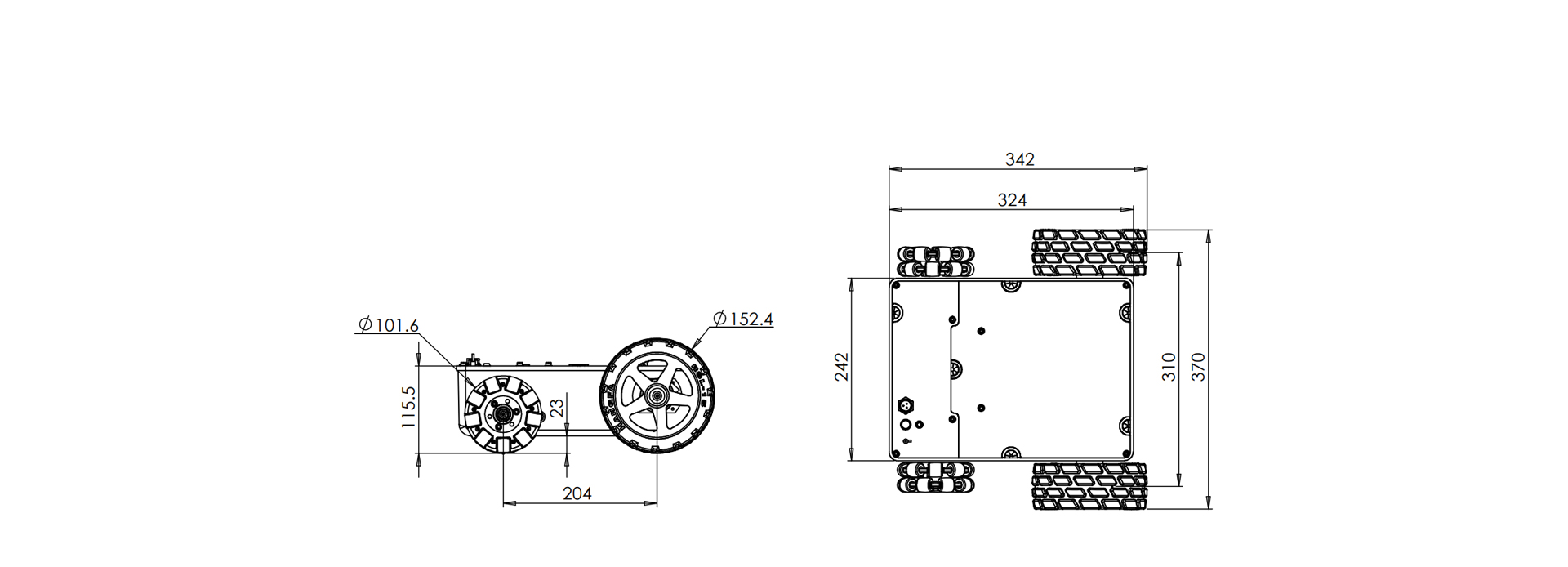
Specification Parameters
Fuselage Form | Aluminum alloy one-piece molding | Overall Dimension | 342×370×115.5 |
Driving Wheel | HSL-15 Rubber Wheel | Diameter of Driving Wheel | 152.4mm |
Driving Method | Two-wheel independent drive | Suspension Form | Rocker arm suspension with driven wheels |
Minimum Ground Clearance | 23mm | Weight | 8.5kg |
Rated load Capacity | 20kg | Motor Type | Hollow Cup DC Servo Motor |
Motor Rated Power | 30W | Motor Encoder | 500 lines/revolution, A and B phase outputs |
Number of Motors | 2 | Motor Drive | Servo drive, CAN bus, RS232 communication interface |
Maximum Travel Speed | 1.2m/s | Maximum Rotation Speed | 370°/s |
Minimum Turning Radius | 0m | Adaptable Terrain | Indoor and outdoor concrete and asphalt pavements with fewer potholes |
Typical Endurance | Approx. 10h (load 10kg, operating speed 1m/s, operating rate 70%) | Standby Time | >30h |
On-board Power Output | 5V@2.5A / 12V@2.5A / Battery voltage (22.4~29.2V)@:5A | Power Fuse Preset Specification | 5×20/10A |
Battery | 24V/7.8Ah lithium-ion battery | Battery Quick Change | Support |
Charger | Input:AC220V~240V / Charging current:3A / Interface:Plug-in type | Accessory | Battery charger, ULB-1 ultrasonic transducer × 5 |
DEMO Board | RHF407 development board (CAN×2, RS232×2, TTL×1, RS485×1, SPI×1, I2C×1, ADC×8, DAC×2, PWM×8, LED×2, keypad×2, independent I/O×24, reusable I/O×29, TF card interface×1, RTC backup battery holder, reusable TFT LCD interface×1) |
Fuselage Form | Aluminum alloy one-piece molding | ||
Driving Wheel | HSL-15 Rubber Wheel | ||
Driving Method | Two-wheel independent drive | ||
Minimum Ground Clearance | 23mm | ||
Rated load Capacity | 20kg | ||
Motor Rated Power | 30W | ||
Number of Motors | 2 | ||
Maximum Travel Speed | 1.2m/s | ||
Minimum Turning Radius | 0m | ||
Typical Endurance | Approx. 10h (load 10kg, operating speed 1m/s, operating rate 70%) | ||
On-board Power Output | 5V@2.5A / 12V@2.5A / Battery voltage (22.4~29.2V)@:5A | ||
Battery | 24V/7.8Ah lithium-ion battery | ||
Charger | Input:AC220V~240V / Charging current:3A / Interface:Plug-in type | ||
Overall Dimension | 342×370×115.5 | ||
Diameter of Driving Wheel | 152.4mm | ||
Suspension Form | Rocker arm suspension with driven wheels | ||
Weight | 8.5kg | ||
Motor Type | Hollow Cup DC Servo Motor | ||
Motor Encoder | 500 lines/revolution, A and B phase outputs | ||
Motor Drive | Servo drive, CAN bus, RS232 communication interface | ||
Maximum Rotation Speed | 370°/s | ||
Adaptable Terrain | Indoor and outdoor concrete and asphalt pavements with fewer potholes | ||
Standby Time | >30h | ||
Power Fuse Preset Specification | 5×20/10A | ||
Battery Quick Change | Support | ||
Accessory | Battery charger, ULB-1 ultrasonic transducer × 5 | ||
DEMO Board | RHF407 development board (CAN×2, RS232×2, TTL×1, RS485×1, SPI×1, I2C×1, ADC×8, DAC×2, PWM×8, LED×2, keypad×2, independent I/O×24, reusable I/O×29, TF card interface×1, RTC backup battery holder, reusable TFT LCD interface×1) |
Typical Components
-
HSL-15 inflatable rubber wheel
-
QL-10 omni wheel
-
HFmotor-3230 coreless DC servo motor
-
IMDR4 servo motor
-
RHF407 development board
-
ULB-1 ultrasonic range-finding sensors
Typical Research and Application Areas
- Pattern recognition technology research
- Electronic engineering experiment
- Carrying and storage applications
- Route planning technology research
- Mechanical engineering experiment
- Monitoring and investigation application
- Automatic driving technology research
- Embedded system development and experiment
- The robot competition
- Sensor technology research
- Image process technology research
- Mapping application
- Artificial intelligence research
- Multi-robot cooperation technology research
- Flexible manufactur system application
Optional Accessories
- HMC-1 remote control handle
- LPC-16 patrol sensor
- ULB-1 ultrasonic range-finding sensors
- Laser radar
- GPS locator
- Kinect device body sensor